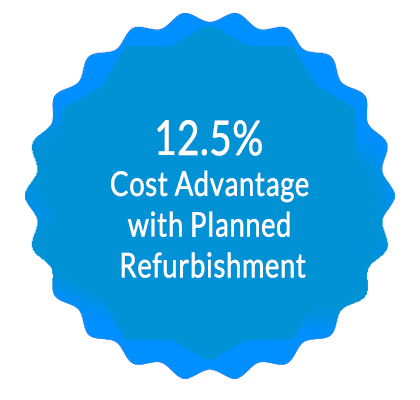
Our service engineers provide hands-on support from tool development to the end of the tool's life. This includes installation support, responsive troubleshooting and planned refurbishment to maximize the uptime of your tools.
Of course, in case of an incident we are here when you need us. But you can influence the service life of your mold and hot runner yourself through planned maintenance and above all, avoid unproductive downtime!