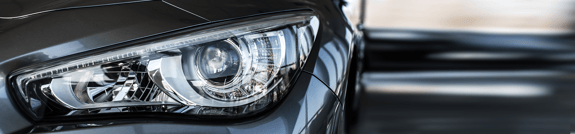
Automotive styling is continuously changing. New technologies are allowing designers to be more creative with lighting both for the exterior and interior of vehicles. The front end is becoming a transparent element to facilitate laser headlamps and various sensors while the rear is evolving with OLED panels. Inside the vehicle light pipes enable ambient lighting systems offer a palette of colors and patterns, allowing drivers to create an atmosphere that suits their style.
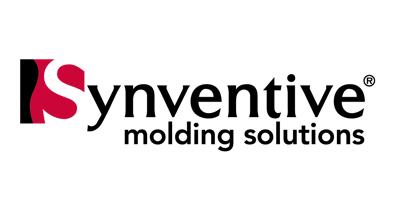
Synventive has responded to these trends by developing the necessary high quality but compact hot runner systems that these complex applications require.
Despite the compact dimensions, threaded nozzle solutions, efficient pneumatic actuators and prefinished valve pins are easy to integrate into the mold. Every Synventive system for lighting goes through rigorous additional quality checks during production to ensure perfect performance every time.
Lighting Case Studies:
Head Lights
- Head Fog Light
- Head Light
Head Fog Light
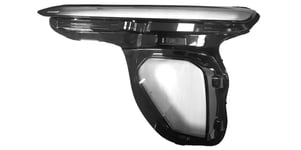
Material: PC
Part Weight: 910 g
Shot Weight: 1820 g
Wall Thickness: 2.5-3 mm
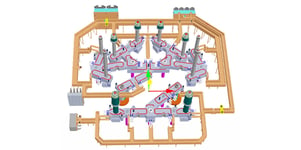
Nozzles: 22E, 16E
System: 2+8-drops,PB8016
Cavities: 2
Gating: Direct
Head Light
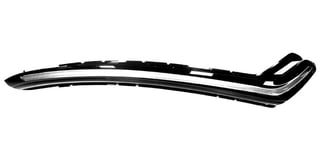
Material: PC-AL2447
Part Weight: 427 g
Shot Weight: 854 g
Wall Thickness: 3 mm
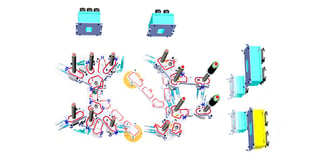
Nozzles: 16E-VSP
System: 12-drops,PNC7518-M04
Cavities: 2
Gating: Direct
Lighting Case Studies:
Rear Lights
- Long Rear Light
- Rear Light
Long Rear Light
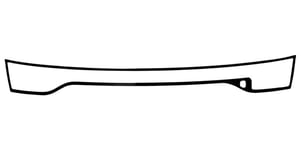
Material: PMMA 8N
Part Weight: 800 g
Shot Weight: 800 g
Wall thickness: 2.5-3 mm
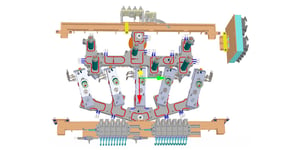
Nozzles: 12E06-VTW, 16E04-VSP
System: 6+5 drops, PB8016
Cavities: 1
Gating: Direct
Rear Light
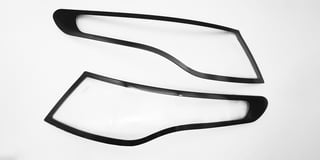
Material: PC/ABS, PMMA
Part Weight: 181 g
Shot Weight: 181 g
Wall Thickness: 2.5-3 mm
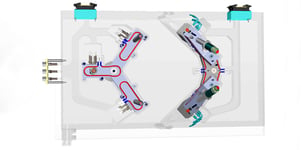
Nozzles: 16E04-VSP-VG, 12E06-VTW-VG
System: 3+2-drops, PB8016
Cavities: 1
Gating: Direct
Lighting Case Studies:
Light Pipe
- Decorative
- Lightguide
Light Pipe
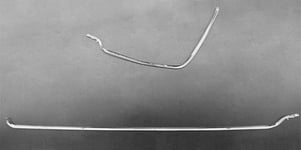
Material: PMMA
Part Weight: 4.08 g + 2.52 g
Shot Weight: 13.2 g
Wall Thickness: Φ3.2mm
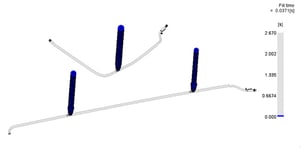
Nozzles: 09E02
System: 3-drops, PNC4508B-01
Cavities: 2
Gating: Direct
Lightguide
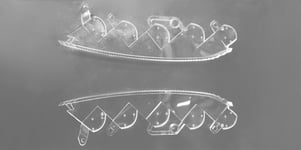
Material: PC Makrolon LED2245
Part Weight: 118 g
Shot Weight: 236 g
Wall Thickness: 5.5 mm
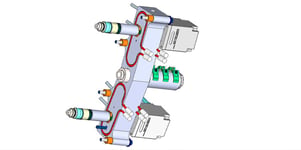
Nozzles: 12E W01V
System: 2-drops
Cavities: 2
Gating: Direct
Lighting Case Studies:
Car Body Lighting
- Light-emitting Grille
- Transparent Grille
Light-emitting Grille
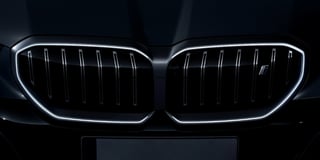
Material: PC / ABS
Part Weight: 250 g
Shot Weight: 500 g
Wall Thickness: 2.5-3 mm
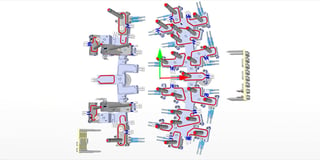
Nozzles: 12E06-VSP
System: 27-drops, HYC4018-M04-R
Cavities: 2
Gating: Direct
Transparent Grille
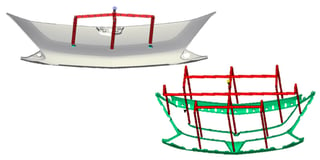
Material: PC Lexan LS1
Part Weight: 2100 g
Shot Weight: 2100 g
Wall Thickness: 3 mm
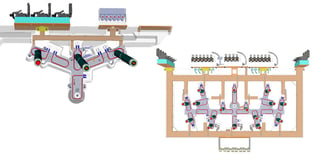
Nozzles: 22E04-VTW
System: 16+3-drops, HB4016
Cavities: 1
Gating: Direct
Perfect Surfaces and Asthetic Gating Points.
Inappropriate gate and geometry configurations can lead to flow interruptions and cause surface defects. With our many years of experience, we make the right decisions when selecting the appropriate nozzle tips and types, as well as the overall design of the hot runner system.
Leakage Free.
For the injection molding of lighting products, we exclusively use threaded hot runner systems, either in thermal or valve gate designs. The use of threaded nozzles allows for precise positioning of components and ensures a homogenous thermal profile. Proper fastening ensures a reliable seal and prevents leaks. Threaded systems also enable easy removal and installation of individual components, significantly simplifying maintenance work.
Approved by our Application Team.
There is no single hot runner nozzle for producing perfect lighting products. Rather, it is the interplay of hot runner configuration, the selection of the right nozzle and gate, and, most importantly, correct geometry and temperature profiles.
Each application is individually examined by the Synventive application team and supported by Moldflow analyses.
Direct Gating.
Direct gating poses particularly higher risk for visible flow lines and gate marks on the surface. However, with careful gate design, these defects can be avoided. With our extensive experience, we typically select a conical needle geometry when direct gating on the visible surface. With the length precisely adjusted and by precise control over the temperature in the gate area, even the most challenging mold designs can be successfully managed!
Temperature Management.
In order to achieve the most uniform temperature profile possible, we use a multi-zone temperature control system. This differentiated precise temperature control has proven particularly effective when combined with threaded nozzles to enable a homogenous thermal profile.
Flow Bore Geometry.
Areas in the hotrunner where the melt changes its flow direction are particularly prone to deposits making them potential weak points for material hangup. We inspect all plugs and transitions for proper fit and sealing, and use endoscopic examination to ensure the quality is maintained and recorded, ensuring correct performance of the hotrunner from the first shot.
You are interested in further information about the Synventive Lighting?